B A S I C B L O C K
TM 5-3805-258-24-1
T E S T I N G
A N D
A D J U S T I N G
1.
2.
Fasten a dial indicator to the crankshaft flange
so the anvil of the indicator will touch the face of
the flywheel housing.
Put a force on the crankshaft toward the rear
before reading the indicator at each point.
8 S 2 3 2 8 D I A L I N D I C A T O R G R O U P I N S T A L L ED
3. With dial indicator set at 0.0 mm (.000 in.) at
location (A), turn the crankshaft and read the
indicator at locations (B), (C) and (D).
C H E C K I N G F A C E R U N O U T O F T H E
F L Y W H E E L H O U S I NG
A. Bottom. B. Right side. C. Top. D. Left side.
4. The difference between lower and higher mea-
surements taken at all four points must not be
more than 0.30 mm (.012 in.), which is the maxi-
mum permissible face run out (axial eccentri-
Bore Runout (radial eccentricity)
of the Flywheel Housing
8 S 2 3 2 8 D I A L I N D I C A T O R G R O U P I N S T A L L ED
1. With the dial indicator in position at (C), adjust
the dial indicator to 0 (zero). Push the crank-
shaft up against the top bearing. Write the mea-
surement for bearing clearance on line 1 in col-
umn (C).
NOTE: Write the dial indicator measurements
with their positive (+) and negative () nota-
tion (signs). This notation is necessary for
making the calculations in the chart correctly.
C H E C K I N G B O R E R U N O U T O F T H E
F L Y W H E E L H O U S I N G
2. Divide the measurement from Step 1 by 2. Write
city) of the flywheel housing.
4-37
this number on line 1 in columns (B) & (D).
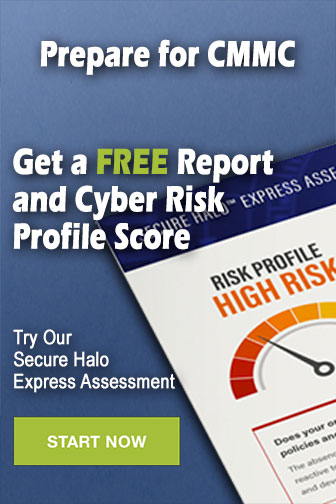